Ring die may be the vital element of pellet mill. It effects the capability consumption, output and quality directly. Statistically, the price of deterioration of ring dies usually counts for 25% from the plant's total maintenance expenses. So selecting the best ring dies is paramount in order to save the price and profit-making. The customers can pick different pellet mill dies when needed. In most cases, when the number of the opening depth and diameter is small, the output is high however the hardness is low.
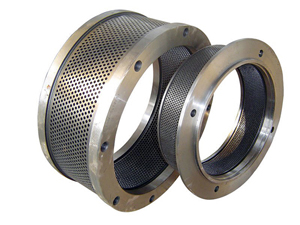
When you're selecting ring dies, there's some fundamental information you need to know. First of all, the ring die includes a wide round shape and it is mounted up and down. Second, pressure of ring die is fixed because within the same diameter mould, the pinch curler of ring die is restricted through the mould diameter. Third, ring die pellet mill switches into machine forced feeding, materials go into the granulating chamber rich in speed rotary and distribute through scraper to make sure feed evenly. Because ring die goes to high rotary speed, the materials damage rate is greater than flat die.
Also you will find benefits of using ring die in pellet mills factory. For example, ring die pellet mills generate less deterioration since the same distance with both inner and outer edges from the curler. The Pelleting process brings extra friction, however this extra friction is a great aspect in producing quality wood pellets for that additional warmth. Additionally, ring die pellet mills will also be more energy-efficient.
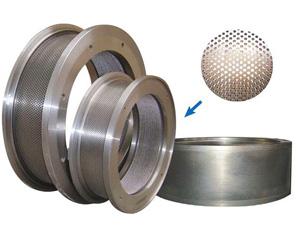
However there are some shortcomings of old type ring die:
Due to the benefits of ring die, ring die pellet mill happen to be adopted in pellet making business for a long time. In the early time, it is usually accustomed to making feed. And recently, wood pellet mill gets increasingly more attention and you will find many producers involve in wood pellet mill making. However, they simply stick to the means by making feed pellet mill after which problems occur, for example low productivity, bad shaping result, serious harm to machine and highly cost. As you may know, wood pellet is harder and want more pressure than feed pellet. That old mode for making feed pellet isn't any more appropriate to top quality wood pellet creating.